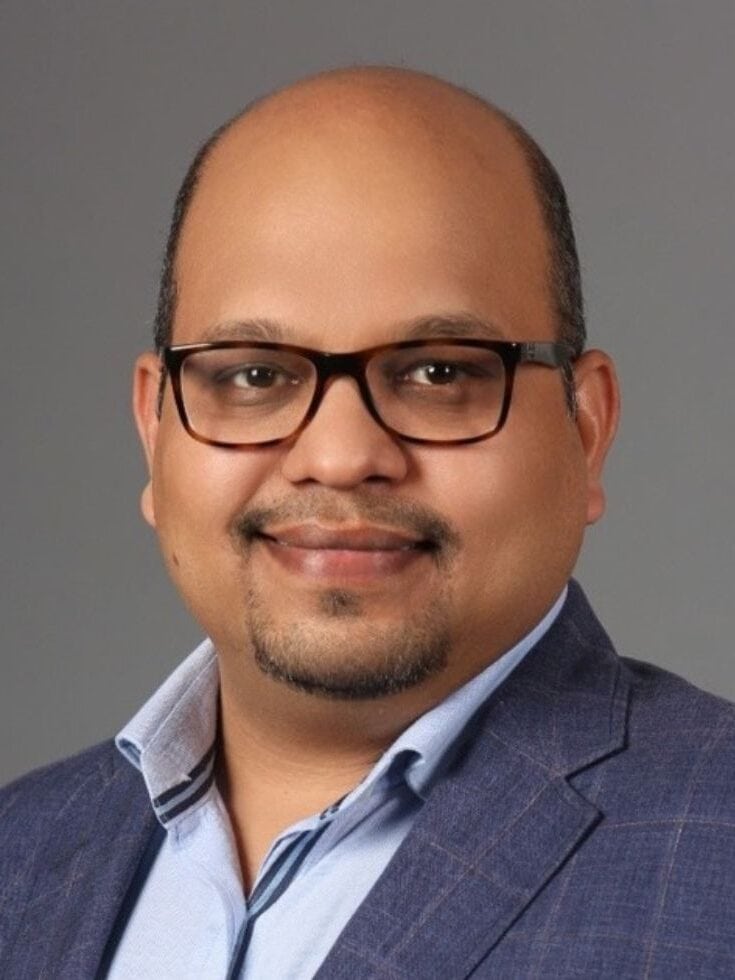
Over the past decade, the economy has shifted its focus from merely providing services to offering enhanced customer experiences. Modern customers now anticipate personalised products and services that are easily accessible across all channels and platforms. To address this challenge, the logistics industry is prioritising automation-driven intralogistics systems that leverage the latest technological advancements to improve operational performance and management.
Changing scenarios
Automation has emerged as a transformative force in intralogistics, countering the drawbacks of antiquated manual procedures that lead to subpar productivity and employee efficacy. By automating repetitive tasks like sorting, picking, and packing, companies can greatly improve precision and output. The deployment of automated systems such as 3D ASRS, conveyor belts, and robotic arms facilitates smooth material flow, enabling faster order completion and diminished lead times. Additionally, automation mitigates the hazard of workplace injuries, fostering safer work settings for employees.
Benefits of technology
Utilising automation uncovers a myriad of benefits, facilitating seamless operations and reducing the likelihood of human errors. Here are some of the benefits:
- Enabling Operational Excellence: Contemporary warehouse operations demand vital flexibility and modularity. New-age intralogistics systems easily combine with existing technologies like automated guided vehicles, conveyors, and 3D-ASRS systems, allowing quick adaptations to changing volumes. Real-time communication and collaboration among cyber-physical systems bolster dependability, efficiency, and planning, resulting in heightened throughput and cost reduction. Predictive maintenance capabilities further curb disruptions and optimise resource utilisation, resulting in significant cost savings.
- Enabling Operations: Today’s intralogistics automation systems can make decentralised decisions, perform autonomous actions, and reduce the need for human intervention. Technologies like smart conveyors and collaborative robots optimise package handling and reduce waste, while predictive maintenance enhances asset availability and performance.
- Improving Performance: Leveraging IoT gateways and real-time data exchange, intelligent intralogistics automation systems furnish workers with pertinent insights. This enriched data empowers employees to make dynamic decisions and streamline warehouse operations.
Furthermore, safety is paramount in the logistics sector, and automation reinforces it through collision avoidance systems, autonomous machinery, and real-time environmental monitoring. Autonomous Mobile Robots (AMRs) and robotic arms can manage heavy loads, diminishing human engagement in risky tasks and elevating overall warehouse safety.
- Meeting Expectations: New-age automation technologies enable quick deployment and response to fluctuating volumes. Additionally, locally controlled smart conveyor systems and robotic arms support mass customisation, efficiently processing tailor-made products without disrupting operations.
Way forward
The integration of intelligent management solutions and automated systems has revolutionised warehouses and distribution centres, substantially enhancing efficiency and productivity. The escalating demand for automated warehousing solutions, fuelled by the growth of e-commerce and online retail, stands as a key factor propelling this expansion.
Automation significantly contributes to sustainability efforts by reducing emissions, optimising space utilisation, and promoting resource savings