Over the years, the warehousing industry in India has undergone a significant transformation from unorganised godown buildings to becoming acknowledged as a major asset category. The pandemic was a true test of this supply chain model because it showed resilience and efficiency in handling surging demand across the country when the entire nation was under a lockdown. The sector was growing because of India’s expanding consumer market, a boom in organised retail, changing consumer behaviours, and regulatory measures. As a result, the pandemic forced the supply chain to be improvised through last-mile delivery, in-city distribution, and several other hybrid methods. All of these required a contemporary warehouse, which is currently a priority for both developers and occupants.
A warehouse is a crucial part of any business’s infrastructure and one of the key elements of the world’s supply chain. According to forecasts, the Indian warehousing industry would grow at a CAGR of 15.64 percent from 2022 to 2027, reaching US$ 34.99 billion (Rs. 2,872.10 billion). In recent years, technological advancements and modern warehouse facilities have transformed India’s warehousing industry. The Indian warehousing sector is expanding due to rising demand and supply over time.
CargoInsights interviews the veterans from the industry seeking their views on the prospects of the warehousing sector.
——————————————————————————————————
Warehousing Firms Turning to Big-Box & Built-To-Suit Solutions
Companies that require complex warehousing, automation, or light manufacturing are increasingly turning to big-box solutions and built-to-suit units for warehouse management, optimised logistics, and streamlined processes.
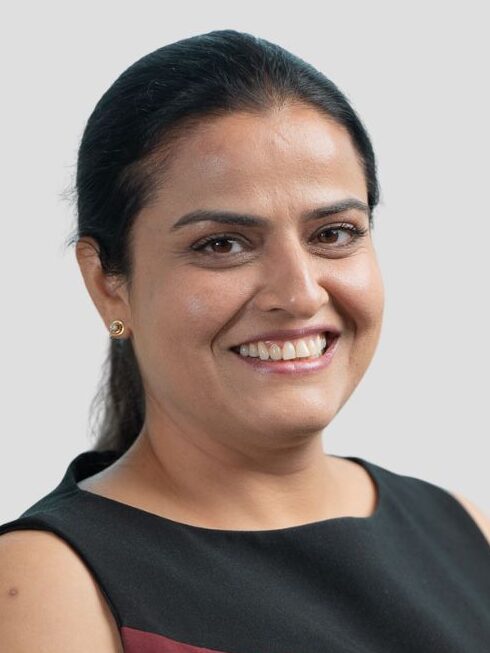
Pooja Malik, Head of Leasing, Horizon Industrial Parks, discusses how the warehousing industry in India has changed and grown in recent years as a result of the rapid expansion of the e-commerce sector, the government’s “Make in India” programme, the implementation of GST, and the growing demand for faster, more efficient supply chain management. Customers want high-quality, compliant, ecologically friendly, and technologically advanced facilities inside fully managed logistics and industrial parks that offer a wide range of services and solutions to a wide range of businesses.
Built-to-suit facilities, multi-story buildings, and in-city warehousing are some of the significant developments affecting the warehousing business. Because of their potential for vertical extension to maximise land utilisation, multi-story and in-city warehouses offer substantial advantages in space-constrained urban locations. Multi-city warehouses provide speedier delivery times to meet consumer demands for same-day deliveries due to their close proximity to urban centres.
Companies that require complex warehousing and automation (e-commerce, chemicals, cold chain) or light manufacturing (auto, components, engineering) are increasingly turning to big-box solutions and built-to-suit units for warehouse management, optimised logistics, and streamlined processes.
Another key trend is the preference for partnering with organised developers such as Horizon, which are dedicated to offering safe, fully compliant, and environmentally sustainable warehouses as well as renewable energy solutions. This assists tenants in risk mitigation, reducing the environmental impact of their operations, and reaching their ESG goals.
Overcoming challenges
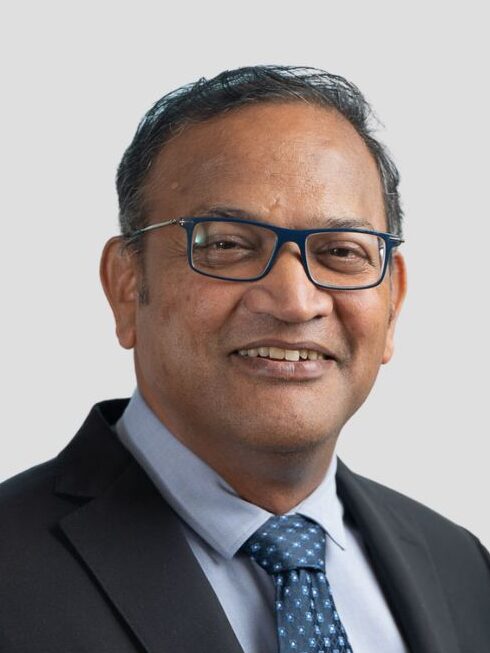
RK Narayan, President, Strategy & Business Development, Horizon Industrial Parks, discusses the primary difficulties encountered by India’s warehousing business, including infrastructure, regulations, and workforce, and how they are being addressed. He explains that the Indian warehousing industry faces a number of challenges that must be overcome in order for it to attain its full potential.
The mere implementation of regional-level development plans that have previously allocated new greenfield infrastructure as well as the extension of existing infrastructure for transportation from hubs to demand centres can provide a boost to new industrial and logistics real estate development supply. This will improve the availability of suitable sites for logistics and industrial parks, increasing access to services and facilitating the transportation of commodities. A single nodal body providing land-related clearances in a timely manner, which is one of the industry’s largest issues, can go a long way towards easing the industry’s ease of doing business. The Indian warehousing business confronts various obstacles that must be solved in order for it to reach its full potential.
Warehousing facilities
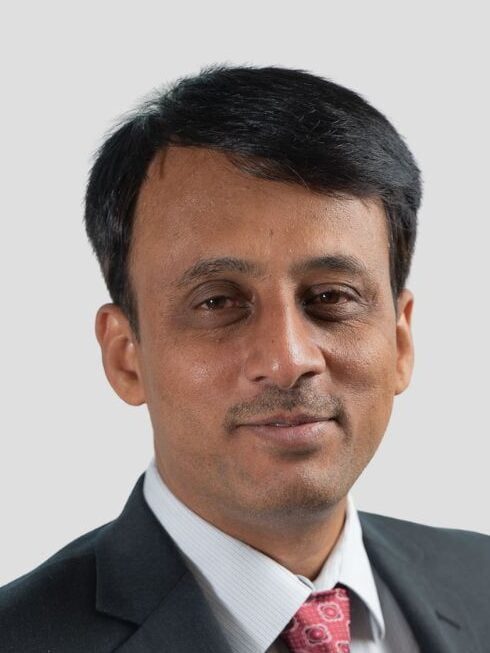
Mahendra Waghule, Head of Projects & Development, Horizon Industrial Parks, outlines the warehousing facilities and services available in India, as well as how they meet the demands of various enterprises. Warehouses can be used for storage and/or light manufacturing, and they can be designed to fulfil the specific demands of various industries. Cold storage facilities for perishable goods, e-commerce fulfilment centres, multi-user warehouses for shared use by third-party logistics service providers, and specialised build-to-suit facilities for the e-commerce, OEMS, and manufacturing industries, such as engineering, automotive, chemicals, and pharma, are examples of warehousing facilities.
Sustainability and environmental concerns
Mahendra Waghule also discusses how the Indian warehouse business is addressing environmental and sustainability issues, such as energy efficiency, waste management, and green practises. To decrease their carbon footprint, warehousing firms are using energy-efficient practises like rooftop solar panels, LED lighting, low-flow water faucets, rainwater harvesting, and the development of Miyawaki woods. Waste management practices such as recycling and waste segregation are also being implemented to minimise the environmental impact of the industry. Apart from this, at the design and construction stages, care is taken to minimise environmental impact by investing in materials with low embodied energy. Institutional developers are also applying for green certifications like IGBC, EDGE, and LEED.
The Indian warehousing business confronts various obstacles that must be solved in order for it to reach its full potential
——————————————————————————————————
Evolution of Warehousing Industry
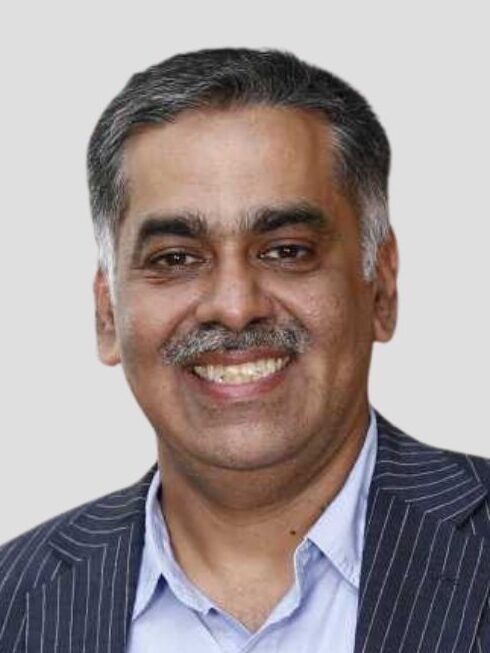
“The warehousing industry in India has undergone significant changes due to changing customer expectations, scaling up of operations, increasing complexity of SKUs, and favourable government policies,” explains Deven Pabaru, Chief Business Officer, Stellar Value Chain Solution.
The significant changes in the warehousing sector have led to a shift towards modern and organised warehousing facilities, with increased demand for third-party logistics providers.
The digital transformation of the sector has also played a crucial role, with technology and automation enhancing operational efficiency, optimising inventory management, and improving overall supply chain visibility. Looking ahead, the trend towards technological advancements is set to continue, with a particular focus on warehouse management systems and low-cost automation. There is also increasing demand for quality and large-scale warehousing spaces, especially in Tier 2 and Tier 3 cities, which is attracting both global and domestic investors. Currently, more than 110 million square feet of Grade A warehouse stock are available across the country, primarily concentrated in the top eight cities, with third-party logistics and e-commerce companies being the primary occupiers of such spaces. This increasing demand presents a significant opportunity for the development of Grade A warehouse facilities in smaller cities.
Other trends shaping the future of the industry in India include a focus on environmental, social, and governance (ESG) standards for warehousing projects, multi-modal connectivity, and dedicated freight corridors to reduce logistics costs. The industry is expected to continue its growth trajectory with a focus on technological advancements, sustainability, and efficient utilisation of resources, contributing to India’s economic growth and development.
key challenges
The warehousing industry in India faces significant challenges that hinder its growth and development. The inadequate infrastructure, including poor connectivity, inadequate storage facilities, and insufficient transportation options, poses a major hurdle. The regulatory challenges, such as cumbersome bureaucratic processes and complex tax structures, further increase the cost of doing business.
In response, the Indian government has taken several initiatives, such as investing in infrastructure development, including dedicated freight corridors and multi-modal connectivity, and simplifying the compliance process through the implementation of the Goods and Services Tax (GST). Public-private partnerships are being promoted to boost infrastructure investment and attract private sector participation in the warehousing sector. To address the workforce challenge, the government is focusing on skill development programs, vocational training, and certification schemes to enhance the skill set of the labour force. Various skill building initiatives are also being taken with engineering colleges to create a trained talent pool.
The collaborative efforts of the government and private sector stakeholders are working towards addressing these challenges and creating a more conducive environment for the warehousing sector’s growth and development in India.
The Indian government has taken several initiatives, such as investing in infrastructure development, including dedicated freight corridors and multi-modal connectivity, and simplifying the compliance process through the implementation of the Goods and Services Tax
Factors driving the demand for warehousing in India
The demand for warehousing in India is driven by multiple factors. Post-GST and post-pandemic, we are at an inflection point and are racing to be very efficient in reducing our overall supply chain costs. Another factor is the shift in consumer preferences towards omni-channel retailing, where traditional warehouses and retail stores are merged into fulfilment centres. Additionally, the development of dedicated freight corridors and improved multimodal connectivity have enhanced the country’s transport and logistics infrastructure, further increasing the demand for warehousing. Furthermore, there is a growing focus on ESG standards and sustainability, which encourages the adoption of green and energy-efficient warehouses.
To meet these evolving demands, businesses in India are increasingly favouring modern grade-A warehousing facilities. These facilities adhere to international standards and offer advanced features such as taller ceilings, cutting-edge technologies (AI, AIDC, ASRS, QR codes), and high-quality flooring for efficient operations. They also prioritise green initiatives, fire safety, mechanised equipment, ample docking stations, and spacious parking areas. Grade-A warehouses provide operational flexibility and effectively meet critical business objectives. The flourishing e-commerce and quick commerce markets, along with the rising demand for robust supply chains across industries, have fuelled the need for grade-A warehousing facilities in India.
To address this demand, the industry is actively expanding the availability of modern and top-notch warehouse spaces. Special attention is given to the six metropolitan cities, which account for a substantial portion (60%) of the capacity. In addition, the industry is investing in technology and automation to optimise operations, reduce costs, and enhance customer satisfaction.
Types of warehousing facilities
There are several types of warehousing facilities and services offered in India, catering to the needs of various industries. Some of the common types of warehouse facilities include ambient temperature-controlled warehouses, cold storage facilities, bonded warehouses, and container freight stations.
For e-commerce, the warehousing industry in India offers specialised fulfilment centres, which help to efficiently manage and process orders, as well as last-mile delivery facilities. For the FMCG sector, the industry provides multi-user warehouses that enable companies to store and distribute products efficiently across multiple locations. The automotive industry requires specialised warehouses that are equipped to handle the storage and handling of heavy machinery and equipment.
The warehousing industry in India also offers value-added services such as kitting, labelling, and repackaging, which help to customise products and prepare them for distribution. Additionally, the industry is adopting new technologies such as real-time inventory tracking and RFID tagging, which enable companies to monitor their inventory levels and improve supply chain visibility. Overall, the warehousing industry in India is highly adaptable and constantly evolving to meet the specific needs of various industries.
Technological advancements and innovations
The Indian warehousing industry has been undergoing significant technological advancements and innovations in recent years, with automation being a major trend. Many companies are using automated material handling systems, conveyor belts, and sorting machines to automate their processes, with robotics performing tasks like palletising, picking and packing, and goods transportation. IoT technology is being used to track and monitor inventory levels, equipment performance, and energy consumption.
These technological advancements have had a significant impact on warehouse operations, helping companies minimise errors, reduce costs, and improve turnaround times. They have also enabled warehouses to operate 24/7, increasing throughput and improving customer satisfaction. As a result, we can expect to see continued investment in these technologies in the coming years.
Technological advancements have had a significant impact on warehouse operations, helping companies to minimise errors, reduce costs, and improve turnaround times
——————————————————————————————————
Rise of Warehousing in India’s Booming Economy
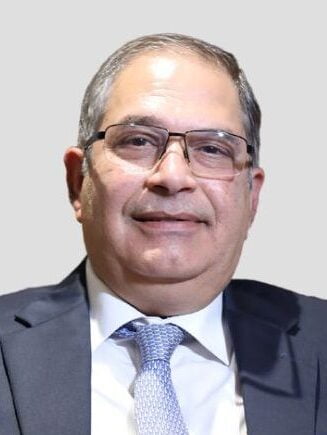
The Indian warehousing sector has seen a remarkable transformation, evolving from unorganised godown structures into large facilities providing high-quality storage and logistics services, says Homi Katgara, Partner, Jeena & Company.
Investments in logistics and organised warehousing witnessed substantial growth and the forthcoming development of multimodal logistics parks is sure to contribute to the development of additional warehousing zones. In recent times, we have seen some free trade warehousing zones start their operations in full swing.
Having said that, India’s warehousing industry is still nascent compared to that of the United States and European countries. However, the industry is exhibiting signs of growth with significant support from central government initiatives such as the National Logistics Policy and Gati Shakti.
Some observed trends are:
Increased digitization: Technology adoption is on the rise. With the implementation of warehouse management systems, automation, and robotics, warehousing in today’s day and age is way more techno-centric.
Infrastructure modernization: the development of infrastructure, including dedicated freight corridors, multimodal logistics parks, modern logistics hubs, and free trade warehousing zones, enhances connectivity and reduces transit times.
Expansion of Multimodal Logistics Parks (MLP): Logistics parks are gaining momentum as they integrate various modes of transportation for seamless connectivity, making the entire process hassle-free for logistics players. The increased traction has shot up the demand for warehousing.
Focus on sustainability and green warehousing: Green practices are actively supporting the reduction of environmental impact and improving operational efficiency.
Challenges faced by the warehousing industry in India
In the recent past, we have come a long way in developing the warehousing industry in India. However, any massive change needs time and patience. Hence, we still have a few challenges to overcome:
Lack of skilled and specialised personnel: It has become a significant concern, particularly given the rise in volumes, intricate operations, and mounting work pressure that involves multitasking. The industry is recognising that finding the right balance between technology and ongoing training of the existing workforce will be crucial to overcoming the lack of skilled personnel.
Inadequate infrastructure: Lack of infrastructure has always been a big challenge and it continues to be one, especially in terms of transportation networks and storage facilities. To address this, the government is already focusing on the enhancement and development of efficient infrastructure.
Regulatory compliance: Companies face the challenge of managing a wide range of compliance requirements that are spread across different areas such as finance, taxation, secretarial, commercial, labour, environment, health and safety. Additionally, they also have to navigate through numerous industry-specific compliance obligations. Businesses should adopt smart and automated compliance solutions to enhance control, visibility, and proactive management of regulatory requirements.
India’s warehousing industry is still nascent compared to that of the United States and European countries
Types of warehousing facilities
In India, there are various types of warehousing facilities and services catering to the needs of different industries. Here are some common types:
General warehousing: Multipurpose facilities that provide storage and handling services for a wide range of products such as e-commerce, FMCG, automotive, and electronics.
Cold storage facilities: Such facilities store perishable goods like fruits and vegetables, dairy products, pharmaceuticals, and frozen food at controlled temperatures.
Bonded warehousing: Allows imported commodities to be stored under customs supervision without prompt payment of duties and taxes.
Distribution centres: Concentrate on effective order fulfilment and product distribution, strategically situated to ensure on-time deliveries to specified regions or markets.
Consolidation warehousing: These are hubs for the process of consolidating smaller shipments into larger, more cost-effective ones.
Warehousing by the hub and spoke: Central hubs receive items from suppliers and distribute them to regional or local spokes.
Automated warehousing: Advanced technology, machinery, and conveyor systems are used to optimise storage, retrieval, and order processing.
Industries like e-commerce, FMCG, automotive, retail, pharmaceuticals, healthcare, electronics, industrial manufacturing, agriculture, food processing, and numerous others benefit from these warehousing facilities and services in multiple ways. Most of our warehouses are equipped to cater to the requirements of a plethora of industries.
Sustainability and environmental concerns
With the advent of technology, businesses now have access to new tools for sustainable logistics and supply chain management. They are realising the potential of implementing environment-friendly strategies not only for reducing their carbon footprint but also for lowering operational costs through enhanced efficiency and waste reduction. The government is actively promoting sustainable practices in the industry, encouraging the adoption of energy-efficient transportation methods, greener fuels, and the construction of multimodal logistics parks to support multimodal transportation. Moreover, the industry is poised to increase its commitment towards developing green logistics infrastructure as a result of the government’s strong focus on green energy and sustainability in the 2023 budget.
“It gives me immense pleasure to mention that we are an environment-conscious company and are strongly focusing on sustainability in our daily operations. Through our environment-friendly initiatives, we have been able to save more than 700 trees in the last fiscal year,” states Homi Katgara.
Addressing training needs
Warehousing businesses in India are taking proactive steps to meet the industry’s skilled worker shortage and training demands. To improve the skills of the existing personnel, in-house training, development activities, and certification programmes are being conducted and promoted by warehousing companies in India. “At our organisation, we make sure that everyone receives regular training to satisfy our standards for service delivery. Government-sponsored programmes for skill development like the National Skill Development Corporation (NSDC) and the Skill India Mission offer support and funding. Workshops, seminars, and on-the-job training all aid in the industry’s capacity building, according to him.
With the advent of technology, businesses now have access to new tools for sustainable logistics and supply chain management
——————————————————————————————————
Surge of Warehousing in South India
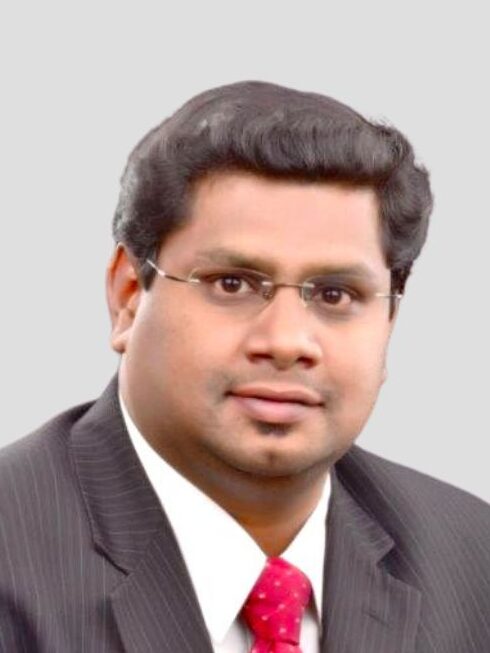
In the words of V. Chandra Kumar, Managing Director, Active Freight Logistics, Vice Chairman, Air Cargo Forum India, Bangalore Chapter, and Secretary, Logistics Club of Bengaluru, the warehousing sector has emerged as a pivotal component in South India’s rapidly growing economy, facilitating seamless storage, distribution, and logistics operations.
Warehousing has seen a considerable increase as a result of the region’s strategic position and robust infrastructure, serving numerous sectors and boosting economic progress. In this section, we look at the emergence of warehousing in South India, its impact on the country’s thriving economy, and the factors that are driving its success.
Infrastructure Development
South India has witnessed substantial infrastructure development, including the expansion of transportation networks, the construction of dedicated logistics parks, and the establishment of industrial corridors. These developments have created favourable conditions for the warehousing sector, enabling efficient movement of goods, reducing transit times, and enhancing connectivity between production centres and consumption hubs.
Government Initiatives
Government initiatives such as the implementation of the Goods and Services Tax (GST) and the “Make in India” campaign have further propelled the growth of warehousing in South India. The unified tax system under GST has simplified logistics operations, eliminated inter-state barriers, and promoted the consolidation of warehouses. Additionally, the “Make in India” campaign has attracted investments, leading to increased manufacturing activities and subsequently driving demand for warehousing facilities.
E-commerce Boom
South India’s tremendous expansion in e-commerce has been a big driver of the warehousing business. The growth of online retail has increased demand for fulfilment centres and last-mile delivery hubs. Warehouses equipped with cutting-edge technology and automation are meeting the demands of e-commerce operators assuring effective order processing, inventory management, and timely delivery of items to customers.
Industrial clusters and SEZs
South India is home to numerous industrial clusters and Special Economic Zones (SEZs) specialising in industries such as vehicle manufacturing, textiles, electronics, and pharmaceuticals. These clusters have drawn both domestic and international investment, resulting in increased demand for warehouse space near manufacturing facilities. Warehouses in or near these industrial clusters provide for more efficient supply chains, shorter lead times, and lower costs.
Focus on technology and automation
The use of technology and automation has transformed the South Indian warehousing sector. Warehouses are incorporating advanced inventory management, order monitoring, and real-time analytics technologies, which are improving operational efficiency and inventory accuracy. Robotics, artificial intelligence, and Internet of Things (IoT) devices are being integrated to further optimise operations, increase productivity, and reduce human errors.
Sustainable warehousing practises
Environmental sustainability is gaining prominence in the warehousing sector. South Indian warehouses are implementing energy-efficient practices such as LED lighting, solar power systems, rainwater harvesting, and waste management initiatives. These sustainable practices not only contribute to reducing environmental impact but also offer long-term cost savings for warehouse operators.
Thus, the warehousing sector in South India is witnessing a remarkable upsurge, driven by infrastructure development, government initiatives, the e-commerce boom, industrial clusters, and a focus on technology and sustainability. The growth of warehousing in South India has provided a robust support system for various industries, optimising supply chains and bolstering economic growth. As the region continues to flourish, the warehousing sector is poised to play an increasingly vital role, further enhancing efficiency, reducing costs, and facilitating seamless logistics operations.
South India’s tremendous expansion in e-commerce has been a big driver of the warehousing business