FM Logistic, founded in France in 1967, is a family-owned independent logistics company with revenue of €1.5 billion in the fiscal year 2022, operations in 14 countries across Europe, Asia, and Latin America, and over 28,000 employees. FM invests in innovation in order to provide logistics, transportation, and go-packing solutions that respond to changing consumer demands.
By acquiring a controlling interest in Spear Logistics, FM Logistic entered the Indian market in 2016. One of the most important 3PL companies in India is FM Logistic. They oversee over 7.0 million square feet of storage space across more than 100 locations. Warehousing and Distribution Logistics services are offered by FM Logistic India for FMCG, Retail, Automotive, E-commerce, Engineering, Telecom, Pharma, and other industries. They offer a wide range of warehousing, distribution, value-added, and omnichannel services through their 5,000+ Indian workers. Many prestigious Indian and international corporations are among FM Logistic India’s exceptionally prestigious clientele. Numerous accolades in the areas of logistics and supply chain management attest to the excellence and dedication they have for their clients. Their goal is to be known as the most dependable and flexible logistics service provider.
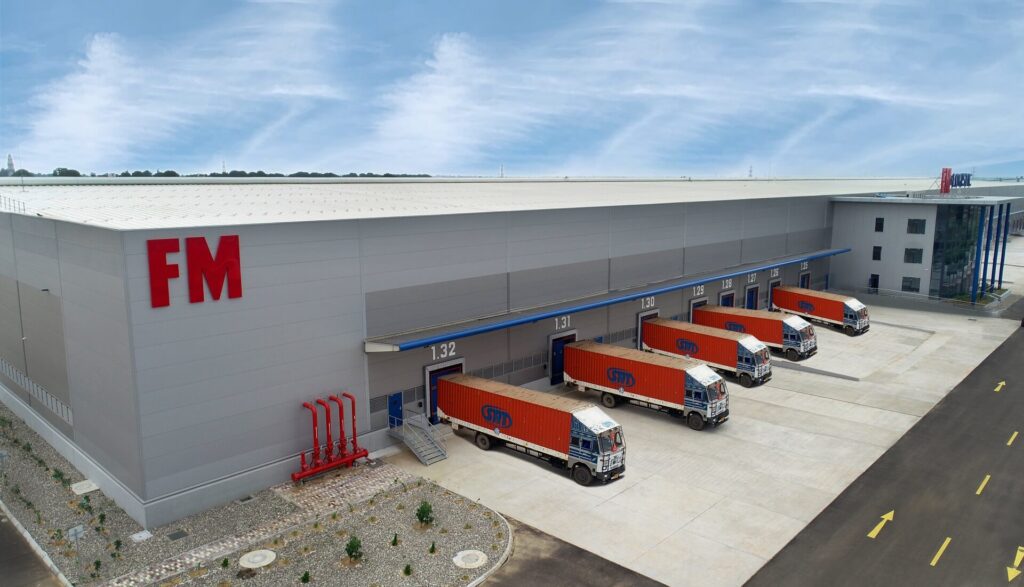
Following are the TOP three achievements of FM Logistic India over the years:
- Growth: FM Logistic India has shown 25 per cent YoY growth over the last six years. They oversaw over 2.5 million square feet of warehouse space in 2016. The area controlled today has grown dramatically to 7.0+ million feet. To provide their current international clients in the consumer goods, retail, and health industries with top-notch multi-customer, multi-activity warehouses nearby India’s largest consumption centres.
The two MCFs in Mumbai (with an extension under construction) and Delhi NCR (next to Gurugram) are already up and running.
FM Logistic in India has not only invested in transportation and warehousing activities, providing better warehousing and distribution services to its customers, but also invested in the digitalisation of its various functions.
At Farrukhnagar, close to Gurugram, the company started operating its first Multi-Client Facility (MCF) that it owned this year. The best LEED-rated logistical facility in the nation, this new A+ building is India’s first LEED Gold-certified warehouse. The MCF has a built-up area of 700,000 ft2, and it has strategic access to the Kundali, Manesar, and Palwal expressways, allowing for quick accessibility to all of the key consumption centres in the North. The MCF offers a designated area for co-packing and other value-added services and has a storage capacity of 100,000 pallet positions. The MCF provides cost-effective quality, storage, and handling services and is outfitted with best-in-class safety and security features.
FM Logistic in India has not only invested in transportation and warehousing activities, providing better warehousing and distribution services to its customers, but has also invested in the digitalisation of its various functions, notably its WMS (Warehouse Management System) and TMS (Transport Management System) that offer high-quality service and real-time visibility to customers.
- Quality Deliverables: FM Logistics prioritises measurable quality deliverables. FM Logistic has emphasised the importance of understanding customer needs and making quick decisions. KPIs and SOPs govern all of their warehouses. Their inventory accuracy is greater than 99.98 per cent across all of their warehouses. FM Logistics manages over ₹ 45 billion in inventory and processes 12 million lines per year.
- Long Term Partnership Approach: FM Logistic India has a substantial client base that includes several blue-chip Indian and multinational corporations. Several Logistics and Supply Chain Management awards have been bestowed upon the company, demonstrating the quality and focus that it brings to its customers. Its vision is to be known as the most dependable and responsive logistics service provider in the industry.
Companies have realised the value of having a real-time pulse on the market and are investing in Grade-A warehousing facilities in smaller cities.
Mars Chocolates was FM Logistic’s first customer in France when it opened its doors in 1967. Today, 53 years later, the association remains strong and has spread to various locations where the chocolate manufacturer operates. Spear Logistics’ very first customer was Atlas Copco. Even after the acquisition, Atlas Copco remains a valued customer of theirs.
70 per cent of our clients are world leaders in their respective industries and markets. This achievement is a result of various deliberate customer-centric measures like:
- Extreme focus and action orientation to address customer concerns on an urgent basis.
- Measurement of possible customer concerns before and as they come up and present solutions to clients for resolution.
- A centralised audit team to audit inventory and processes.
- Structured MIS and monthly review meet with customers.
- Specialised team of industrial engineers to:-
- Make processes leaner and more efficient for cycle time reduction.
- Customise systems and workflow customisation
- Facilitate manpower planning and training

Concerns in warehousing
Alexandre Amine Soufiani, Managing Director, FM Logistic India, in an exclusive interview with CargoInsights, explains the challenges faced by the warehousing sector, “Despite rising demand, logistics in India has many difficulties, such as cost pressures, excessive returns, and subpar infrastructure.
Insufficient integration of transportation networks, information technology, and storage and distribution facilities is the industry’s biggest problem right now. National, regional, and municipal authorities apply regulations at a number of different levels. However, the laws vary from city to city, making the development of national networks difficult.
Both the industrial and retail industries, which are particularly poor at a practical level, such as IT, driving, and warehouse, as well as at a higher strategic level, both require trained labour. There is a shortage of qualified management and customer service staff due to the chaotic structure of the Indian logistics business, the notion that it is a manpower-intensive sector, and the absence of suitable training schools. High levels of loss, damage, and stock deterioration are caused by inadequate facilities and management, particularly in the perishables sector. Lack of training and inadequate specialised equipment, such as appropriate chilled storage and containers, are both contributing factors to the issue. Although academics and practitioners are already aware of the significance of logistics and supply chains, research in the area is still in its infancy. National, regional, and local governments set regulations, yet they vary from city to city, leading to a broken network.
National, regional, and municipal authorities apply regulations at a number of different levels. However, the laws vary from city to city, making the development of national networks difficult.
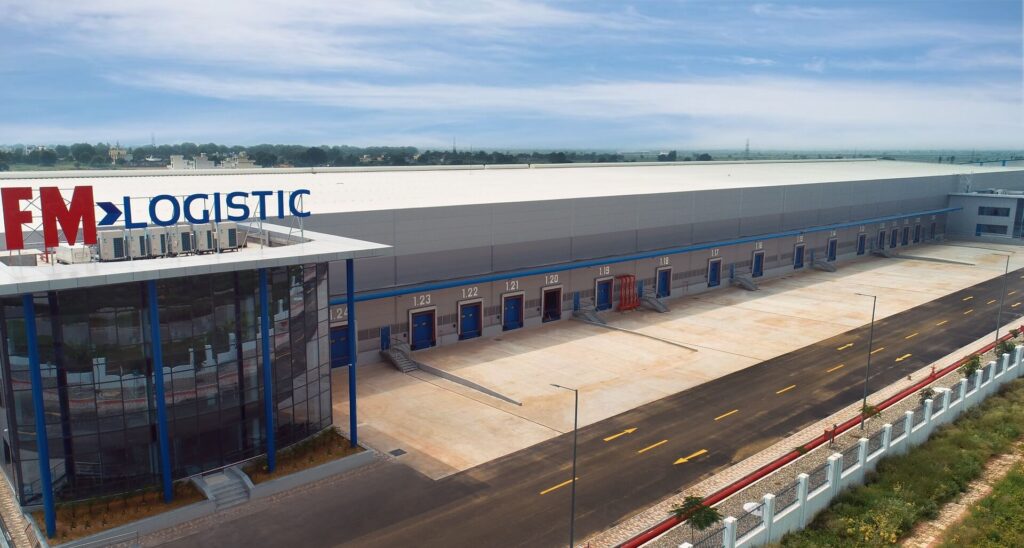
Role of Grade-A warehouse
Over time, the Indian storage and logistics sector has grown significantly in terms of both size and scope. The days of warehousing being limited to providing goods storage space and basic handling are over. Businesses today are searching for logistics service providers who can help them grow closer to their end customers by incorporating more technology, process, and automation into their warehousing solutions. The dynamics of the logistics industry have altered as a result of a shorter time to market and rising demand from the time-sensitive e-commerce sector. The logistics industry has improved in both organisation and standardisation. Grade A warehouses and the increasing use of technology are the stepping stones in this process, as they provide ease in time-bound supply, customer satisfaction, and a risk-free environment.
The demand for Grade-A warehouse facilities across the nation has been boosted by the burgeoning e-commerce business and strong demand for the improvement of retail supply chains across industries. More specifically, the ongoing COVID-19 pandemic has increased the need for high-quality warehouse space. This growth has been fueled by omnichannel operations and e-commerce. Since the majority of consumers in the country, including those in Tier 2 and Tier 3 cities, have turned to online shopping, there has been a significant shift in consumer behaviour. The things that customers today need must be available to them as soon as possible and when they need them. Companies have realised the value of having a real-time pulse on the market and are investing in Grade-A warehousing facilities in smaller cities to deal with such scenarios. This has made it easier for them to serve the city’s continually expanding consumer base. Rapid technological advancement is transforming business operations in the logistics industry.
Future
FM Logistic in India will consolidate its position over the next five years by providing a global offering of end-to-end supply chain services such as warehouse management, primary transportation,Multi-Client and secondary distribution, and value-added services. They endeavour to manage 10 million square feet of warehousing space, with the majority of warehousing services provided from their Multi Client Facilities. They are working hard to establish themselves as the Indian leader in technological advancement, skill development, and sustainability.
FM Logistic India has set the goal of becoming the market leader in contract logistics in India. They have all of the success ingredients: global expertise, long-term vision, skilled people, client trust, operational know-how, the ability to innovate, the strength of new Multi-client warehouses, and so on. Their warehouses are set up to provide omnichannel services—a combined solution for B2B and B2C channels from the same location.