Karan Vohra shares insights on how FMCG warehouses use historical data, predictive analytics, and strategic layouts to manage fluctuating demand, optimise processes, and ensure compliance and efficiency.
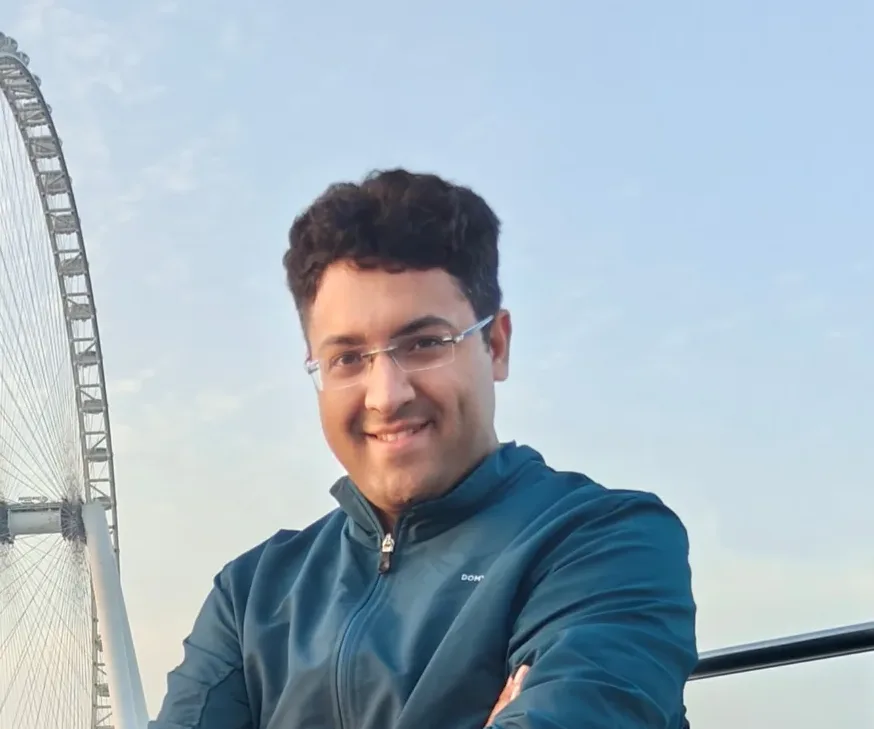
FMCG warehouses optimise picking and packing through strategic warehouse layout and zoning
In the fast-paced world of FMCG, managing fluctuating demand is a critical challenge. Karan Vohra, Supply Chain Manager, Customer Service—North India and Nepal, Colgate-Palmolive, shares valuable insights into how FMCG warehouses rise to the occasion. By blending traditional insights with modern tools, these warehouses leverage historical data and predictive analytics to anticipate demand peaks and valleys. AI-based solutions enable proactive resource management, ensuring agility and preparedness. This fusion of tried-and-true methods with advanced technologies keeps FMCG warehouses responsive and ready to meet ever-changing market demands.
Optimising picking and packing
FMCG warehouses optimise picking and packing through strategic warehouse layout and zoning. High-volume, fast-moving goods are strategically placed closer to dock areas to minimise picker movement and expedite turnover. Conversely, slower-moving SKUs are designated to advanced pick areas, ensuring safety stock proximity for efficient outbound vehicle turnover. This zoning strategy enhances productivity and expedites turnaround times, crucial for managing high-volume FMCG goods efficiently.
Efficient inventory management
In FMCG warehouses, effective inventory management for perishable products hinges on just-in-time replenishment and strict inventory controls. Emphasising small batch sizes and rapid turnover minimizes obsolescence costs. Seamless IT integration facilitates accurate demand forecasting and robust supply chain planning, crucial for handling perishable items efficiently. This approach integrates precise demand sensing and agile manufacturing strategies, ensuring FMCG warehouses maintain optimal inventory levels despite shorter shelf lives and expiration concerns.
Ensuring compliance and accuracy
To ensure compliance with regulatory standards, FMCG warehouses adhere to guidelines set by regulatory bodies. Each product is assigned a unique batch, code, or lot number in accordance with regulations, enabling precise tracking throughout the supply chain journey. Advanced technologies such as Warehouse Management Systems (WMS) and barcode scanning enhance accuracy and compliance, integrating seamlessly to maintain high standards. Regular third-party audits validate adherence to regulations, ensuring product integrity and consumer safety are prioritised throughout FMCG warehouse operations. These measures underscore the commitment to robust tracking systems and regulatory compliance in the handling of FMCG goods.
Designing effective warehouse layouts
FMCG warehouse layouts prioritise resource efficiency and productivity. Segmentation based on volume and billing rates categorizes inventory into ABC and FSN classifications. A 3×3 matrix zoning strategy further enhances efficiency in handling and storing FMCG products, ensuring optimal utilisation of warehouse space and streamlined operations.
Collaborative strategies
Effective collaboration among FMCG warehouses, suppliers, and retailers is essential for ensuring uninterrupted product flow and timely deliveries. Maintaining clear expectations, continuous monitoring, and utilising Management Information Systems (MIS) for service level oversight are critical. Additionally, GPS-enabled track-and-trace systems, transportation management systems, and proactive alerts enhance transparency and customer satisfaction. The integration of a logistics control tower provides a centralised dashboard for reviewing performance, ensuring efficient coordination across the supply chain.
Conclusively, through strategic insights and advanced technologies, FMCG warehouses ensure efficiency, compliance, and collaboration, prioritising integrity and customer satisfaction in dynamic markets.