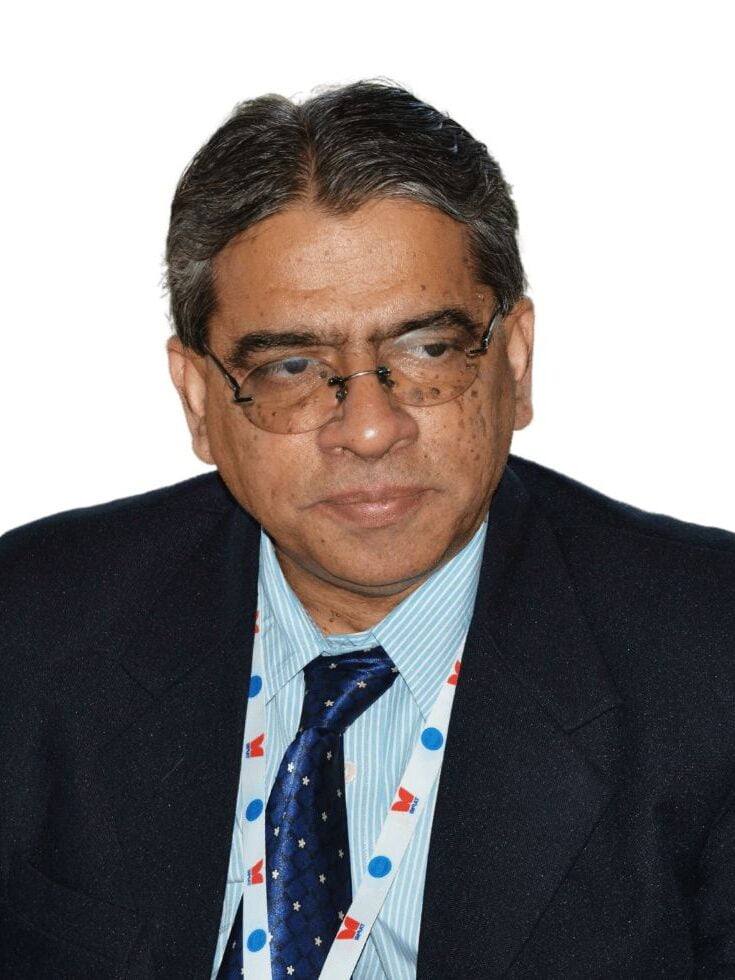
Warehousing’s historical core responsibility has been the storage of goods. However, the scope and core responsibilities of warehouse management operations have evolved to deliver high-level inventory management, swift receiving and shipping dock management, accurate and flexible customised pick & pack services, and state-of-the-art storing and safekeeping solutions for all goods.
Due to the development of an increasingly integrated global economy market with production facilities scattered around the globe, warehouse operations are becoming a key factor to cope with demand variations; making inventory management a critical component of a company’s financial performance.
What is Lean?
The lean way of thinking was developed by Toyota for automotive manufacturing. Since their operations include processes such as receiving, put-away, picking & packing, and dispatch, etc., the lean methodology is also being applied to warehousing. In the context of warehousing, the idea is to eliminate those processes and activities that are absorbing resources but are not creating any additional value. This is done by applying the 5S system of lean, which are Sort, Straighten, Shine, Standardise, and Sustain, to the processes and procedures of the warehouse. The need for lean methodology in warehouses can be best understood in the context of the challenges that warehouse managers face every day. Here are a few of the major ones:
- Reducing operational costs
- Coping with the pressure of shorter lead times
- Increasing the number of perfect orders
- Meeting the target of same-day deliveries
- High attrition rates and the rising cost of labour
- Managing multiple delivery channels
- Managing an increasing number of SKUs
- Shortage of space
- Seasonal/fluctuating demands
However, these are only a few challenges that crop up in the face of the rising prospects of commerce. While on a broad level, lean will lead to better efficiency, reduced errors, and maximum asset optimization, here are a few specific goals that lean can help achieve:
- Standardizing workflow, resulting in shorter order processing time
- Optimizing asset utilization by finding the right place for the right inventory/equipment
- Eliminating inefficiency in material handling, thus reducing labour and transportation costs
- Stocking as per demand, thus enabling easy tackling of seasonal demand
- Cutting time wastage- helping you achieve a higher rate of perfect orders and same-day/next-day deliveries
- Standardized processes which make it easy to manage and assess multiple SKUs
As warehouse digitalization becomes more promising and traditional warehouses are disrupted, lean warehouse management is a simple yet effective way to attain transformation and competitive advantage. It also means that you can tap technology to improve your lean warehouse since digitisation is also all about simplifying and making processes more efficient.
The idea behind lean warehousing is to eliminate processes and activities that are absorbing resources but are not creating any additional value