Kartik Jalan, CEO, INDICOLD, shares compelling insights on overcoming cold chain challenges across sectors like pharma, FMCG, seafood, and agriculture through innovative strategies, smart packaging, and collaborative, tech-driven last-mile solutions.
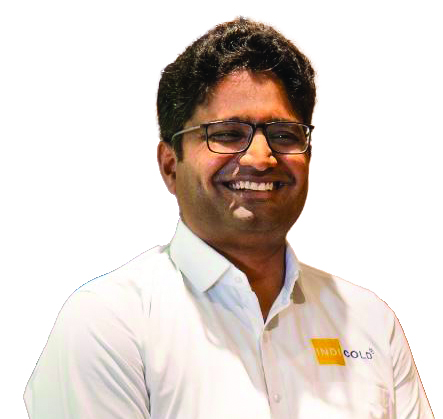
The most powerful strategy is collaboration
As global temperatures surge and regulatory requirements evolve, cold chain logistics face mounting pressure across vital sectors like pharmaceuticals, FMCG, agriculture, and seafood. Kartik Jalan, a leading voice in cold chain management, brings a pragmatic yet forward-looking perspective to tackling these multifaceted challenges. According to him, the primary disruptor today is heat—especially for pharmaceuticals that demand a precise 2–8°C environment. “A single break in that range can compromise product efficacy,” he emphasises.
Regulatory pressures
What adds further complexity are stringent international compliance standards such as the EU’s Good Distribution Practice (GDP) and the FDA’s Food Safety Modernisation Act (FSMA), which demand real-time temperature monitoring and traceability. “The challenge in India is not just static cold storage—it’s end-to-end cold chain movement. Uneven infrastructure, power outages, and transit delays can unravel the integrity of the entire system,” Jalan notes. Industries like seafood and FMCG also suffer disproportionately due to high cooling and packaging costs, making reliability an expensive proposition.
Smart solutions
So how are cold chain providers navigating these vulnerabilities? Jalan highlights a combination of technology, infrastructure, and partnerships. “Many companies are now integrating solar and battery backups to safeguard against power outages, which is particularly critical for pharmaceuticals and dairy,” he shares. Artificial intelligence is being used to dynamically adjust routes, avoiding traffic snarls or adverse weather in real time. “That kind of responsiveness can mean the difference between loss and success in a temperature-sensitive delivery,” he adds.
Collaborative advantage
Perhaps the most powerful strategy, though, is collaboration. Jalan stresses that cold chain stakeholders must look beyond silos. “Cold storage is just one link. We need shared logistics, smarter packaging like phase-change materials, and integrated IoT systems to maintain consistency from farm or factory to fork or pharmacy.” He notes that such collaboration doesn’t just mitigate risks—it optimises costs and expands cold chain access.
Last-mile innovations
When it comes to the notoriously tricky last mile, Jalan is candid: “It’s where most breakdowns happen, especially in remote areas.” Forward-thinking providers now deploy battery-powered portable cooling units and even drone-based delivery for time-critical, lightweight shipments like vaccines or fresh seafood. Micro-fulfilment centres positioned closer to consumption points cut transit times dramatically. In rural regions, solar-powered storage units hold products safely until local delivery teams take over using insulated boxes.
End-to-end visibility
“Real-time monitoring and smart packaging close the loop,” Jalan says. “We must not think of cold chain as isolated warehouses or refrigerated trucks. It’s a living network—and every link matters.”
In a warming world with soaring consumer expectations, this adaptive and collaborative approach sets a compelling example of how innovation can keep the cold chain unbroken.