Ranjit Kumar, National Head, Leasing, Pragati Warehousing, emphasises sustainable design with solar panels and rainwater harvesting. Future-ready warehouses prioritise automation with FM2 flooring and high clear heights, enhancing efficiency and adaptability to industry needs.
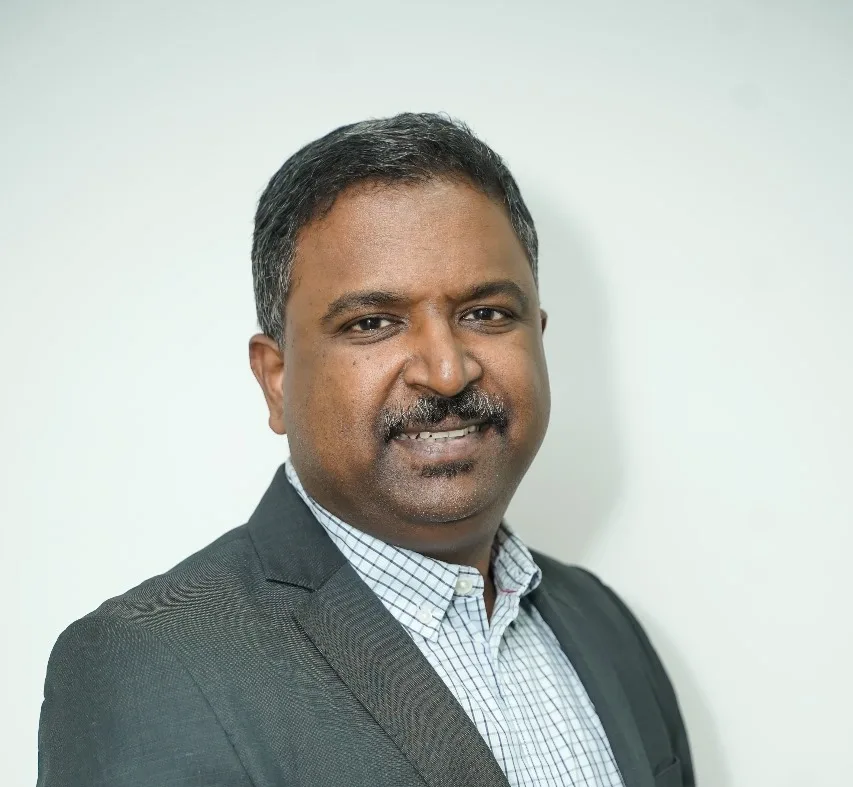
The pivotal emphasis is on scalable design principles, ensuring seamless integration with advancing technologies
Ranjit Kumar emphasises sustainable practices in warehouse design and construction. For him, sustainability is paramount in Grade-A facilities, ensuring strict environmental compliance and minimising ecological footprints. Important elements comprise solar panels for renewable energy, rainwater harvesting for water conservation, and advanced sewage treatment for responsible waste handling. Additionally, there is a focus on extensive plant landscaping to boost biodiversity, fostering environments that are not only efficient but also ecologically beneficial. This strategy underscores a dedication to ensuring warehouses are resilient to future challenges through innovative, environmentally aware design concepts.
Automation Readiness
When developing a Grade-A warehouse poised for future automation, the pivotal emphasis is on scalable design principles, ensuring seamless integration with advancing technologies. Essential factors include cutting-edge infrastructure and features, such as:
1. FM2 flooring to facilitate the smooth movement of bots and automated guided vehicles (AGVs), reducing downtime and maximizing productivity.
2. Spacious layouts with large bay spaces allow for easy manoeuvrability of automated systems, enhancing safety and operational efficiency.
3. Ample clear height supports vertical storage solutions, enabling efficient navigation of automated material handling systems.
Innovative warehousing design
Efficient warehouse layouts optimise space and material flow through innovative design principles. These include:
- Efficient Park Planning: Wide, well-maintained internal roads facilitate smooth vehicle movement, minimising congestion and ensuring safe circulation of goods, boosting productivity.
- Increased Loading/Unloading Docks: Strategically positioned docks manage high volumes of goods efficiently, with cross-docking layouts enhancing throughput between trucks.
- High Load-Bearing Capacity: Floors designed to bear over 6T/sq m optimise storage and movement of heavy goods and machinery, maximising space utilisation. These principles not only enhance operational efficiency but also future-proof warehouses for evolving industry demands, emphasising scalability and functionality.
Industry-specific warehouses
The nature of a client’s business profoundly shapes the design and functionality of warehouses. For manufacturing clients, warehouse layouts become highly customised based on their specific industry. These specialised needs often require additional features compared to a standard warehouse. Conversely, retail warehouses prioritise streamlined throughput with minimum internal handling time. Easy material movement inside the building and the park is crucial for swift order processing.
Future warehousing
Warehouses are playing a crucial role in future supply chains, which will rely heavily on automation and AI systems. They are evolving from storage hubs to pivotal components of global trade, optimising supply chains, stabilising prices, and adapting to market demands. Grade-A warehouses epitomise this transformation by providing a future-proof infrastructure that incorporates hyper-automation and advanced technologies to enhance efficiency and productivity. Additionally, the focus on sustainable warehousing, with green building practices and energy-efficient operations, underscores their shift from cost centres to transformation centres.
By embracing innovation and sustainability, warehouses are poised to redefine global supply chains as dynamic engines of efficiency and transformation.