A crucial component in the supply chain that connects the producer and the final consumer is logistics and warehousing. The reach, time to market, and cost reductions that show to be significant enabling factors for businesses to remain relevant in today’s ultra-competitive climate are determined by the effectiveness of a company’s supply chain. This is especially true in the digital age, where companies are continuously pressured to reduce expenses and turnaround times in order to attract and keep customers.
While precise demand estimates are the cornerstone of this endeavour, the efficiency of the logistics chain determines how much money and time may be saved. The demand for continuous inventory cycle reduction has evolved the warehouse’s role from a simple storage depot to a virtual pit-stop that supports inventory management, secondary packing, cross-docking, and product extraction in the shortest amount of time.
Multi-Modal Logistics Parks
Logistics costs in India account for 13–17% of GDP, which is approximately double (6–9%) the logistics cost-to-GDP ratio in rich nations such as France, Hong Kong, and the United States. Much of the discrepancy in logistics costs can be traced to India’s lack of efficient intermodal and multimodal transport infrastructures, which serve as the backbone of these industrialised nations’ logistics supply chains. A comparison of India and the United States reveals a significant disparity in road freight costs per tonne per km (ptpk): the cost in India (adjusted for Purchasing Power Parity) is INR 1.9 per tonne per km, about double that of the United States.
Key Factors Responsible for Higher Logistics Cost in India
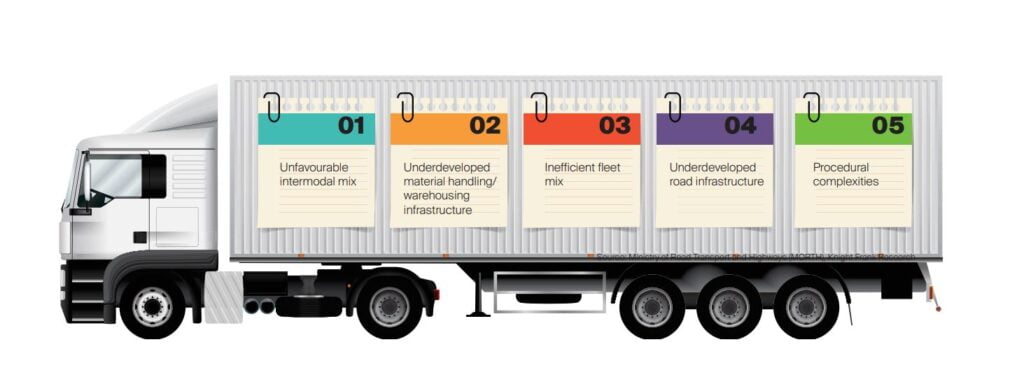
To alleviate some of these inefficiencies, the Ministry of State Transport and Highways (MORTH) has begun the creation of multimodal logistics parks (MMLP) throughout 35 nodes in the country, which account for over 60% of the country’s freight traffic.
An Estimation for 15 of These Regions Which Account for Close to 40% of the Freight Movement in the Country Has Been Detailed Below:
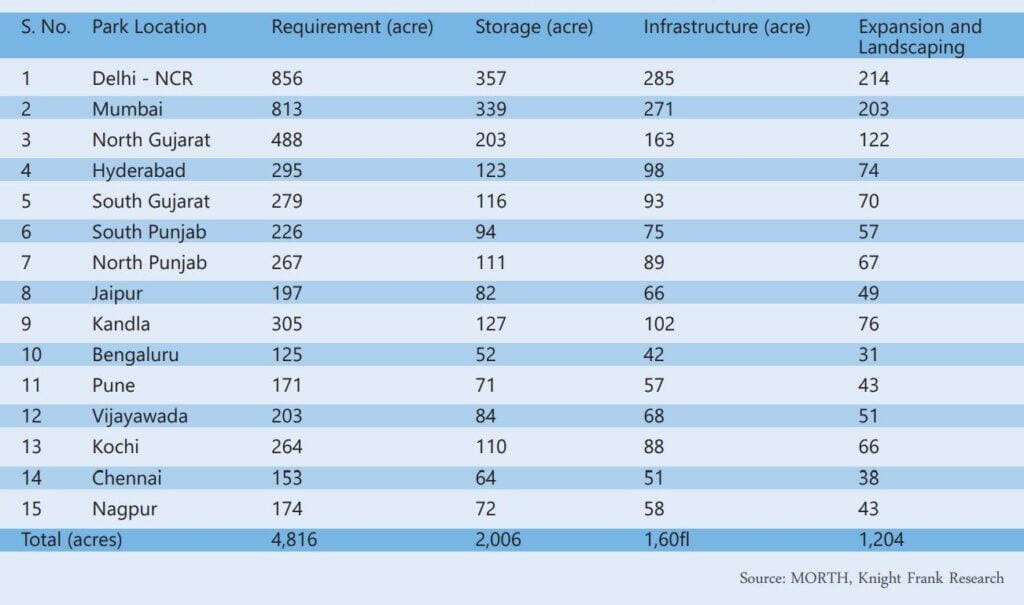
The MORTH is developing Multi-Modal Logistics Parks (MMLP) through an umbrella SPV named National Highways Logistics Management (NHLML).
These multimodal logistics parks are expected to serve four key functions.
Logistics in India – Existing and Ideal Scenarios
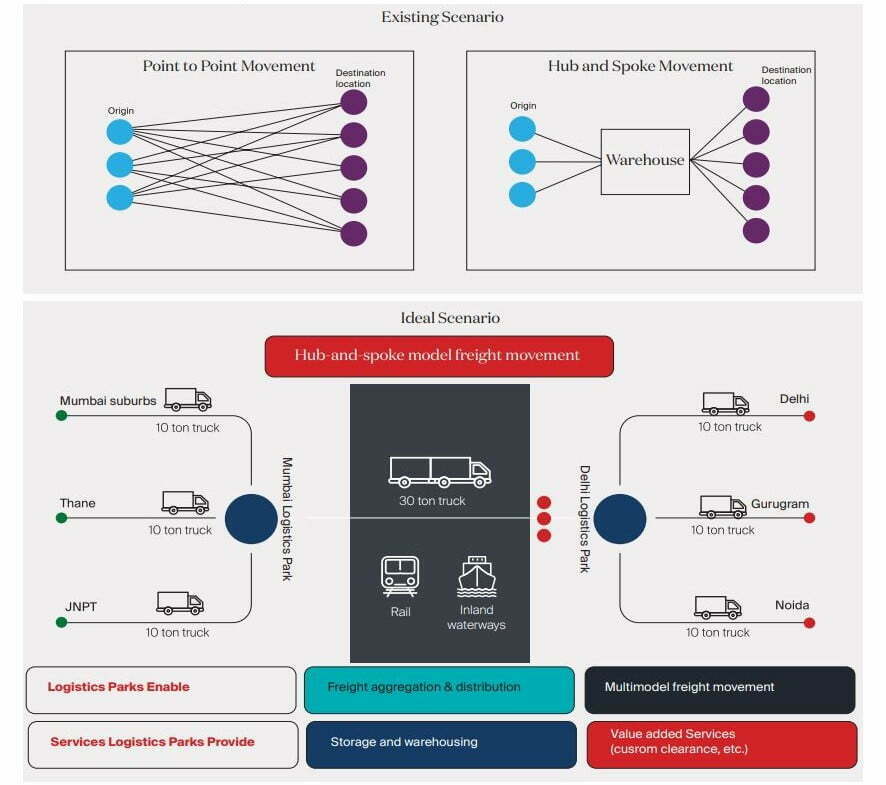
- Freight aggregation and distribution – Logistics parks are often established outside of urban agglomeration zones to serve as freight transportation hubs, allowing for freight aggregation and distribution. Logistics parks that serve as freight aggregation and distribution hubs allow line-haul freight transfer (between hubs) on larger trucks, lowering freight transportation costs.
- Multimodal freight transportation – Logistics parks with road and rail access allow for multimodal freight transportation. This allows freight transfer between hubs to shift from road to rail and waterways, lowering freight costs significantly because rail expenses are far lower than road costs.
- Storage and warehousing – It is intended for logistics parks to offer contemporary mechanised warehouse space that satisfies the unique needs of various commodity groups.
- Value-added services – Customs clearance at logistics parks will make it possible to cut down on line-ups at the ports, lowering the cost and length of time for export cargo transit.
Following Are the Advantages of Multimodal Logistics Parks:
Transportation cost reduction: MORTH estimates that logistics parks will enable freight transit on trucks and rail, resulting in a 10% reduction in transportation costs for the top 15 nodes.
Warehousing cost reduction: Due to reduced leases in logistics parks, moving from warehouses currently operated inside city boundaries to those located outside the city limits will permit a reduction in warehousing costs.
Pollution reduction: For the 15 priority nodes, increased freight transportation on bigger trucks and rail will result in a 12% reduction in carbon dioxide (CO2) emissions. Due to reduced fuel use per tonne of travel, heavier vehicles will produce fewer CO2 emissions. On a per-tonne-per-kilometer basis, the CO2 emissions from moving goods by rail are also around 65% lower than those from moving goods by road.
Congestion reduction: According to MORTH, a nearly 20% reduction in freight vehicles will be necessary to accommodate greater freight transportation on bigger trucks and rail to meet the needs of the top 15 nodes. Additionally, moving warehouses and wholesale markets from the city or its expanding outskirts to logistics parks will free up urban spaces and ease traffic congestion.
As pandemic-related anxieties subsided during FY 2022, mobility returned to normal
Warehouse Market Scenario
Given the expanding demands of a sizable consumer market and the strong government-set economic growth targets, the Indian warehousing business has long been regarded as a lucrative investment opportunity. A significant factor influencing interest in the warehousing market is the focus on raising the manufacturing sector’s GDP contribution to 25% by 2025 and developing India into a hub for global design and manufacture through the “Make in India” initiative. Although the investment case is extremely compelling, demand for the nascent storage sector has recently weakened as a result of the economy’s slowdown since FY 2020 and the COVID-19 pandemic in FY 2021.
In FY 2022, when people started to get over their dread of the epidemic, supply chains swiftly recovered and demand surged, which brought a lot of spillover demand back into the market. The market was able to rebound to record levels in FY 2022 despite the significant increase in building costs caused by inflationary forces driving up the rates of essential inputs like steel and cement.
Occupier demand increased 62% YoY to 4.8 million square metres (51.3 million square feet) in FY 2022 as firms caught up and growth plans that had been put on hold due to pandemic-related demands were revived. This also represents a new peak for the Indian warehousing sector in terms of annual transaction volumes, highlighting the market’s robustness, particularly against the backdrop of a still-stabilising economy. Pune and Hyderabad experienced the largest YoY gains in annual transacted volumes at 166% and 128%, respectively, while NCR and Mumbai dominated the market in terms of overall transaction volumes during FY 2022.
Annual Warehousing Transactions
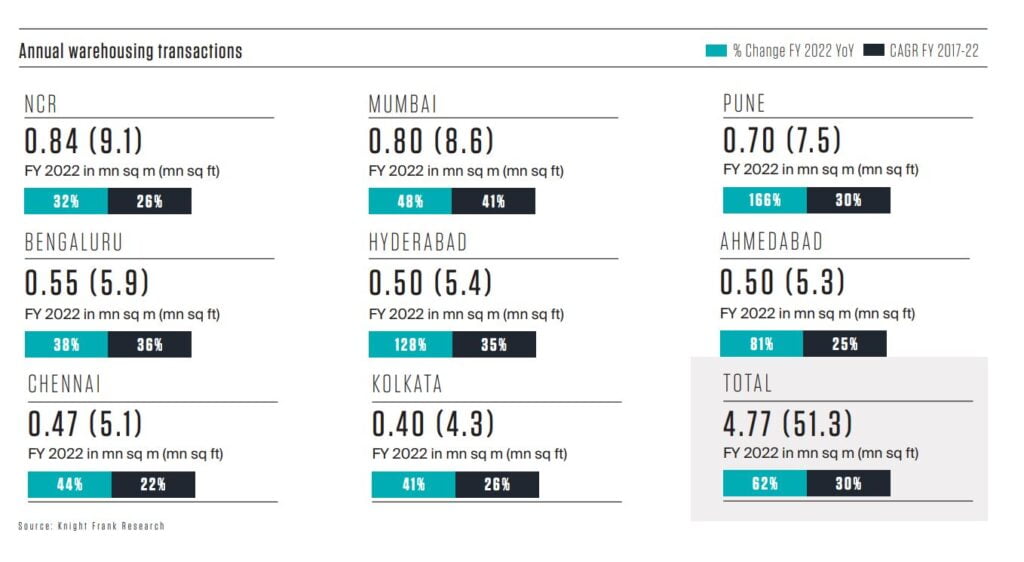
There are 31 storage clusters that make up the eight key markets, and it’s important to note that in FY 2022, more than half of the area transacted took place in five of these clusters in the NCR: Pune, Mumbai, and Kolkata.
Because Grade A facilities are significantly better equipped to handle exigencies like those posed by the pandemic or manage the increased throughput requirements seen in its immediate aftermath, occupants have continued to exhibit a clear preference for them. Some of the aspects that continue to pique occupier interest include the inherent operating efficiencies, adherence to safety standards, and improved contingency planning as a result of the greater competence of workers due to higher institutional participation. Grade A properties continued to be in high demand during FY 2022, making up 64% of the total volume of transactions.
The value adds that Grade A properties bring to supply chain operations have long been sought after by 3PL and e-commerce operators, and their substantial proportion of overall transaction volumes also significantly contributes to the continuing take-up of Grade A properties. 57% of the Grade A spaces occupied during the course of the year were in these two sectors.
With a market share of 29% in FY 2022, the 3PL industry led all occupier categories. The fact that this was less than the 31% recorded in FY 2021 might be partly related to the decline in share of the e-commerce industry, which makes up a sizable portion of a 3PL player’s tenant roster. In FY 2022, the 3PL industry occupied 31% of all available space, all of which was in Pune.
As pandemic-related anxieties subsided during FY 2022, mobility returned to normal. This had a direct impact on the retail sector’s use of warehouse space. Consumer demand increased in hard format stores. The sector’s share increased from 4% in FY 2021 to 11% in FY 2022 as retailers quickly added warehouse capacity to meet the rapid increase in demand.
Stock and Supply
According to the report, India’s eight key markets contained an estimated 35 million square metres (376 million square feet) of storage stock at the end of the fiscal year. The Mumbai market accounted for 42% of this stock, with NCR accounting for the remaining 60%. Strong transaction volumes have reduced vacancy levels to 16% in fiscal 2022. In fact, with the exception of Mumbai and Chennai, vacancy levels in all other areas have decreased significantly.
The development of Grade A warehousing facilities has increased in recent years, accounting for 37% of total stock today, up from 35% in FY 2021. The larger warehousing markets of Mumbai and NCR have a significantly lower share of Grade A warehouses because they are considerably older markets and the majority of their stock was developed before the need for Grade A warehousing gained traction. Because of their core demand base of auto and auto ancillary tenants, Pune and Chennai have the highest concentration of Grade A stock.
In FY 2022, the rising trend of Grade A development continued, with developers increasingly focused on higher-grade park development that is compliant with modern norms and the increased throughput requirements of businesses today. There is also a growing emphasis on improving the aesthetics of these warehouse parks and creating a more pleasant working environment. 52% of the supply coming online in the eight key markets in FY 2022 was in Grade A properties. Six of the eight markets had an increase in the share of grade A stock in FY 2022 compared to the previous year.
The market has undeniably come out of the pandemic’s shadow, and occupier demand has only become stronger as the year comes to a close. Despite concerns about inflation in the global economy, the central bank’s aggressive rate hikes have been successful in keeping inflation under control. Even though businesses in India will be impacted by the global economic climate, the warehousing sector should be supported in FY 2023 because of our economy’s slow but steady improvement and our somewhat improved fiscal situation.
(Source: K night Frank Research )
Given the expanding demands of a sizable consuming market and the strong government-set economic growth targets, the Indian warehousing business has long been regarded as a lucrative investment opportunity