Kladana’s new WMS features improve inventory tracking, order fulfillment, and warehouse operations for MSMEs and D2C brands.
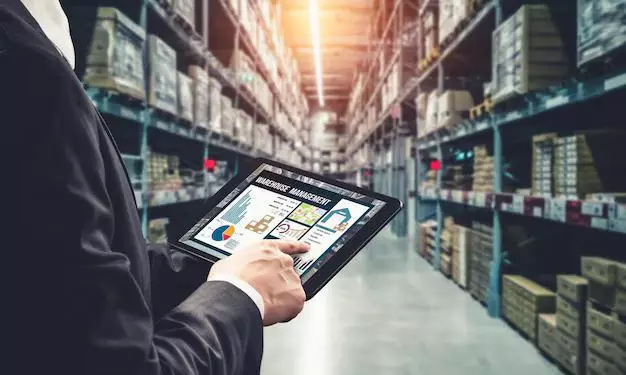
Kladana has launched a significant update to its Warehouse Management System (WMS), designed to optimise inventory and warehouse operations for small and medium-sized enterprises (SMEs). The enhanced module, part of Kladana ERP, introduces advanced tools for managing stock, fulfilling orders, and streamlining warehouse workflows.
Key upgrades include real-time inventory tracking through location-based bin storage, reducing errors and boosting order accuracy. Unique bin identification using zones, rows, and racks enables faster order picking and packing. Additionally, integrated barcode scanning simplifies stock counts and ensures accurate updates directly from the warehouse floor.
The system offers robust reporting features, providing timely insights into stock levels, movements, and overall warehouse efficiency. These updates eliminate the need for multiple tools, helping businesses centralise operations on a single platform.
Aleksandra Brovchuk, Director of Kladana India, emphasised the update’s impact on MSMEs and D2C brands, highlighting benefits like reduced inventory errors and enhanced responsiveness to market demands. Available at no additional cost for paid users, the WMS ensures cost-effective and seamless implementation.