Nitin O Mahipal, CEO & MD, Mega Pack and Carry, emphasises that addressing labour shortages in logistics requires a balanced approach of automation and upskilling, fostering a sustainable workforce while enhancing operational efficiency and productivity.
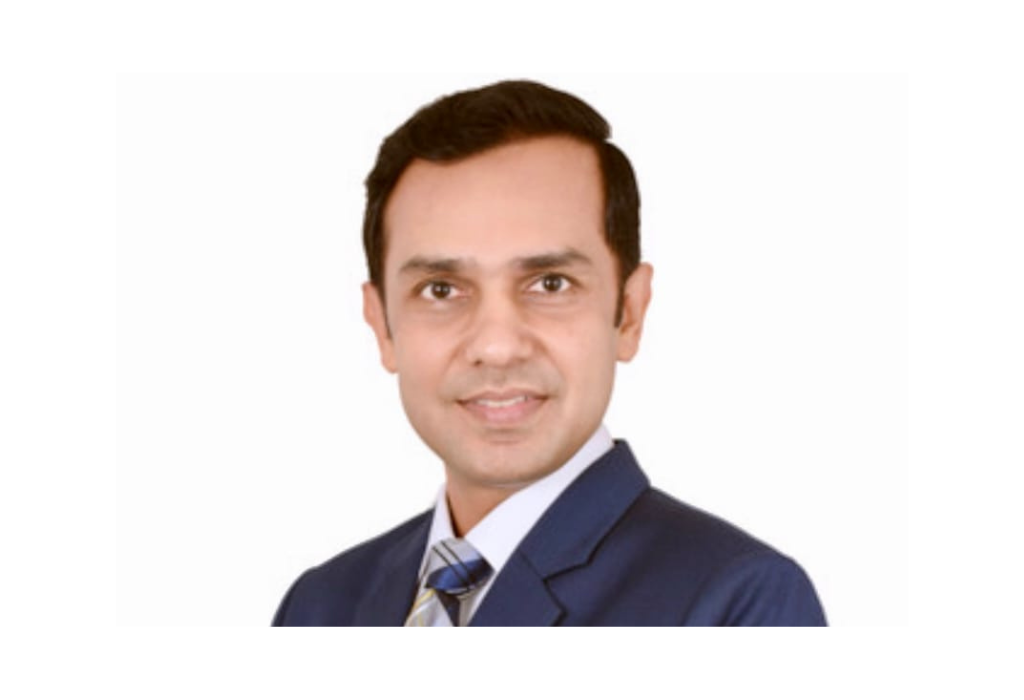
A balanced approach is essential for tackling labour shortages in logistics
Nitin O Mahipal highlights a significant challenge currently facing the logistics sector: labour shortages. The rapid growth of e-commerce, global supply chains, and increasing consumer expectations have led to a higher demand for a trained workforce. Unfortunately, the industry is struggling with persistent labour shortages, exacerbated by high turnover rates and the physically demanding nature of many jobs. To bridge this gap, companies must prioritise automation and upskilling as key strategies to sustain and enhance their operations.
Strategic investments
Small and medium-sized enterprises (SMEs) often face financial constraints, making it essential to invest in solutions that deliver clear returns. By integrating automation into areas with high turnover, businesses can significantly boost productivity and achieve immediate ROI. For instance, automating repetitive tasks in distribution centres, such as scanning, assembling, and shipping, can greatly improve operational efficiency while reducing dependence on manual labor. Comprehensive automation is particularly beneficial for businesses seeking to scale up repetitive processes, as robots can handle physically demanding tasks like picking and packing, allowing human workers to focus on more strategic roles.
Enhancing efficiency
Automation not only replaces manual labour but also enhances the capabilities of existing workers. Companies utilising robots and automated technologies can alleviate labour shortages by automating tedious tasks like tape and label application. This enables employees to engage in critical activities that require human judgement and creativity. Additionally, AI-powered demand forecasting can optimise labour allocation, ensuring resources are used efficiently. The success of these technological solutions often hinges on their collaboration with human workers; for instance, AI-augmented reality can assist less experienced employees by providing step-by-step instructions, boosting confidence and accuracy.
Upskilling workforce
While automation can reduce the workload on human workers, it cannot solve labour shortages alone. A crucial part of the solution is educating and upskilling the workforce to effectively collaborate with new technologies. Investing in training programs is vital for SMEs, as it equips employees with the necessary skills to understand and operate advanced systems. A recent MHI survey indicated that 41% of companies are actively investing in upskilling initiatives for tech-focused supply chain roles, highlighting a growing recognition of the need for skill development in logistics.
Future directions
A balanced approach is essential for tackling labour shortages in logistics. By combining technology with targeted training, companies can enhance employee skills, boost operational performance, and foster a safe and supportive work environment. Emerging technologies not only refine human skills but also enable continuous upskilling in response to evolving industry demands. To build a resilient and efficient workforce, logistics firms must invest in both automation and personnel development, positioning themselves for success in an increasingly complex and competitive market. The future of logistics relies on embracing automation and upskilling as complementary strategies, ensuring a sustainable and future-ready workforce.