Ajit Jangle, Managing Director of FM Logistic India, discusses strategies to enhance warehouse material handling efficiency through improved design, modern technology, and data analytics. Techniques include automation, AI, IoT, demand-driven stocking, and standardisation methods like 5S and Six Sigma.
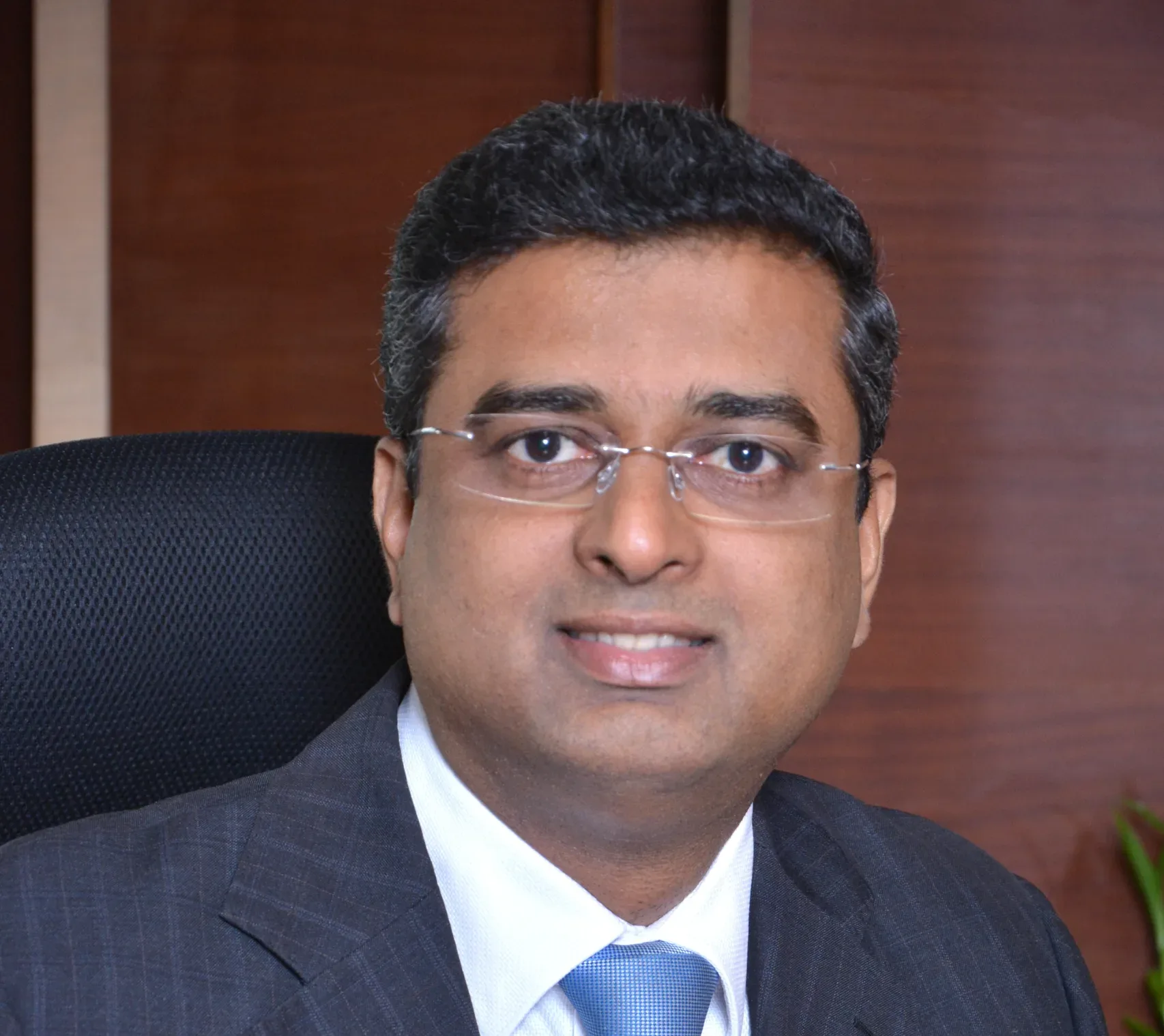
Advancements in technology and equipment have significantly transformed material handling and inventory management practices
Ajit Jangle, Managing Director, FM Logistic India, provides insights into optimising warehouse material handling. In today’s fast-paced and competitive business world, efficient material handling is crucial for maintaining a smooth supply chain and ensuring consumer satisfaction. Key strategies include analyzing current processes, optimising warehouse design and layout, and investing in modern warehouse management systems for real-time inventory tracking and accuracy.
Warehouse efficiency
Advancements in technology and equipment have significantly transformed material handling and inventory management practices. Automating processes such as demand forecasting, replenishment, and inventory control enables businesses to make faster, more informed decisions, ensuring optimal inventory levels. Artificial intelligence (AI) and Machine learning (ML) algorithms analyse vast amounts of data to estimate demand, optimise routes, and efficiently deploy resources, thereby enhancing warehouse management and reducing costs. Automation and robotics simplify tasks like picking, packing, sorting, and maintenance, increasing overall efficiency. Additionally, the Internet of Things (IoT) involves sensors and devices that collect real-time data on goods and equipment within the warehouse, providing comprehensive visibility. This real-time tracking facilitates better inventory management and control, further improving warehouse operations.
Optimising inventory
To optimise inventory flow and minimise storage space requirements, businesses employ several strategies. Demand-driven stocking involves understanding seasonal and cyclical demand variations to accurately forecast future demand, helping to align inventory levels closely with actual demand, thereby minimising excess stock and storage needs. Effective storage strategies include ABC analysis, which categorises inventory into A, B, and C groups based on value, directing resources, and improving stock visibility. Additionally, FSN Analysis categorizes inventory into fast-moving (F), slow-moving (S), and non-moving (N) items. This allows businesses to focus resources on fast-moving items, optimise inventory levels for slow-moving items, and effectively manage non-moving items, enhancing overall inventory management.
Inventory challenges
Common challenges in warehouse inventory management include maintaining accurate stock levels, efficient order picking, and optimising space utilisation. Issues also arise from unreliable suppliers, inventory shrinkage, seasonal demand fluctuations, and handling obsolete inventory. Effective technology integration is crucial. Data analysis plays a pivotal role in overcoming these challenges. By anticipating demand, tracking inventory, and optimising material handling processes, businesses can improve productivity. Analysing material flow trends further aids in optimizing warehouse storage and handling, ensuring efficient operations.
Streamlining operations
To ensure warehouses remain organised and efficient, several methods are employed. Standardising procedures for receiving, storing, picking, and shipping items provides consistency and boosts operational efficiency. The 5S methodology enhances organizations by reducing non-value-added activities and improving workflow. Additionally, the Six Sigma approach focuses on capability building, fostering a high-performance culture that enhances associate efficiency and effectiveness.
By leveraging these strategies and advancements, warehouses can overcome challenges, optimise inventory management, and maintain high levels of efficiency, ensuring a smooth and responsive supply chain.