Discover how trends like e-commerce growth, automation, and sustainability are reshaping warehouse lease agreements. From urban warehouse demands to flexible lease terms, explore insights from industry expert Zafeer Ahmed on navigating this evolving market landscape.
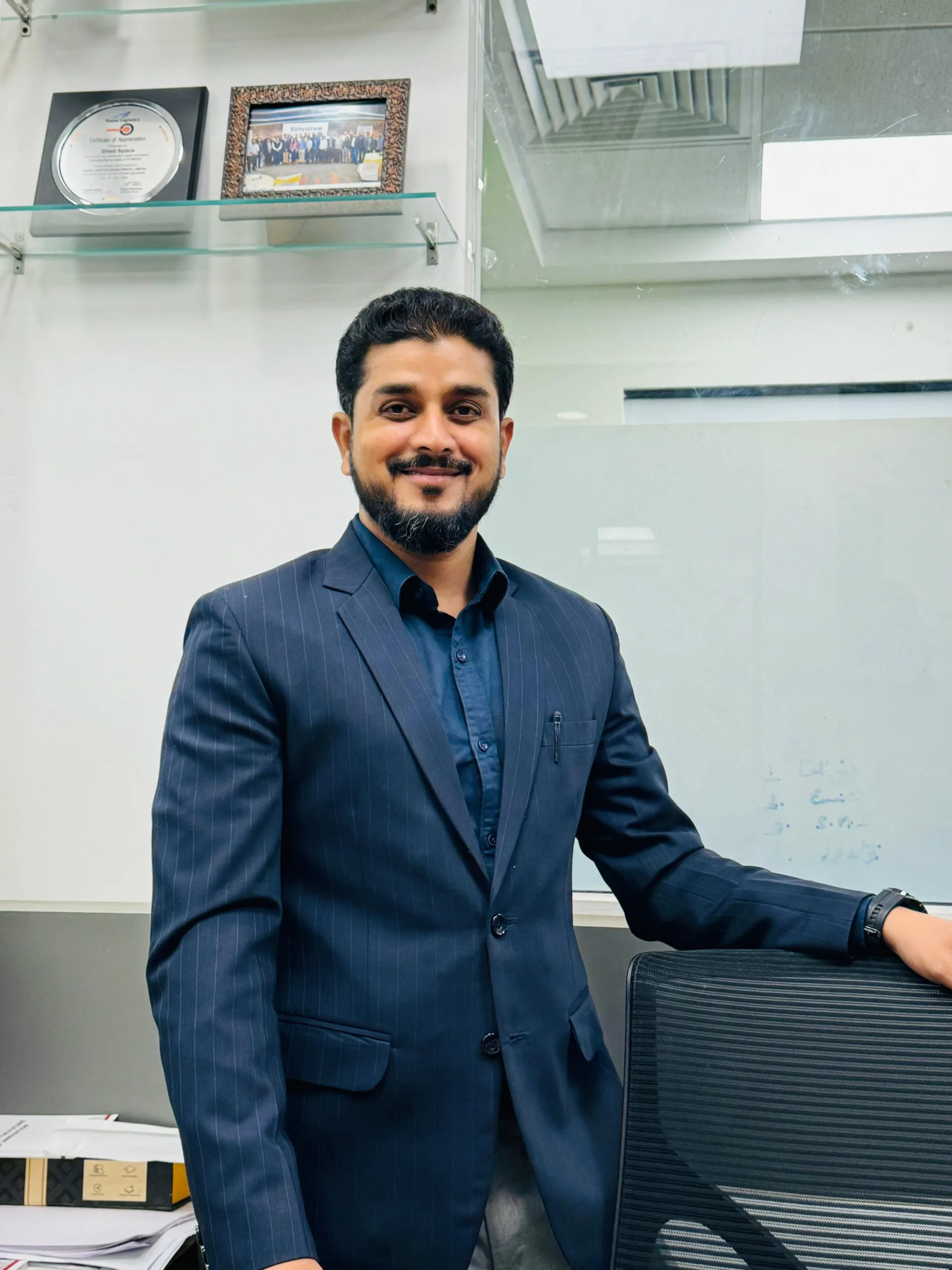
Zafeer Ahmed, Managing Director (IWS), XRE Consultants, offers valuable insights into the evolving landscape of warehouse lease agreements. Today, the market is witnessing transformative shifts fuelled by trends such as the rapid expansion of e-commerce, automation, and a heightened focus on sustainability and safety. The surge in online shopping has escalated demand for warehouse space, influencing lease dynamics with increased rents and reduced vacancy rates. Automation and robotics are now integral, prompting leases to accommodate advanced infrastructure needs like enhanced power capacity and internet connectivity. Businesses are seeking eco-friendly warehouses closer to urban centers to meet accelerated delivery expectations. Flexibility has become paramount, with tenants favouring shorter lease terms and expanded customisation options. Post-COVID, safety and security considerations are pivotal in shaping lease agreements to ensure operational resilience. Ahmed’s insights illuminate how businesses are navigating these trends to optimise their warehousing strategies in a rapidly evolving market environment.
Warehouse innovations
Automation and robotics are now pivotal, reducing errors and boosting picking efficiency. Advanced Warehouse Management Systems (WMS) are optimizing inventory control with real-time tracking capabilities. The integration of IoT, AI, and machine learning has bolstered automation capabilities, transforming warehouse operations. Looking forward, innovations like wearable technology and voice-controlled warehouses are set to further refine these processes, promising heightened efficiency and enhanced safety measures. These advancements mark a significant leap towards smarter, more adaptable warehouse environments, shaping the future of logistics.
Human-automation synergy
Automation in warehousing enhances what humans can do by making tasks safer and more accurate, allowing workers to focus on important jobs. It helps with tasks like improving accuracy, organizing work better, and analysing data more precisely. This reduces stress for workers and helps them maintain a good work-life balance. When building warehouses, automation speeds up construction, reduces waste, and ensures flawless execution alongside human efforts. By blending automation with human skills, warehouses become more efficient, safer, and adaptable. This partnership ensures that people remain crucial to warehouse operations, improving productivity, and preparing warehouses for future challenges in logistics and distribution.
Space optimisation
Maximising warehouse space is crucial for efficiency and growth without building more. Using multi-level racks that fit warehouse height, adding mezzanine floors for extra storage, and Automated Storage and Retrieval Systems (AS/RS) reduce errors and boost efficiency. Designing smart storage with 3D modeling and lean principles minimises wasted space. Flexible racks and modular designs adapt to changing needs, enhancing overall space use. These cutting-edge techniques optimize warehouse functionality, ensuring every inch supports operations effectively. Efficient space management not only meets current demands but also prepares warehouses for future growth and challenges in logistics and storage solutions.