Parminder Singh Bhalla, Managing Partner, Concrete Planners, discusses the critical role of proper flooring in warehouse operations. Selecting the right flooring enhances safety, durability, and efficiency, minimising risks and maintenance costs while boosting productivity.
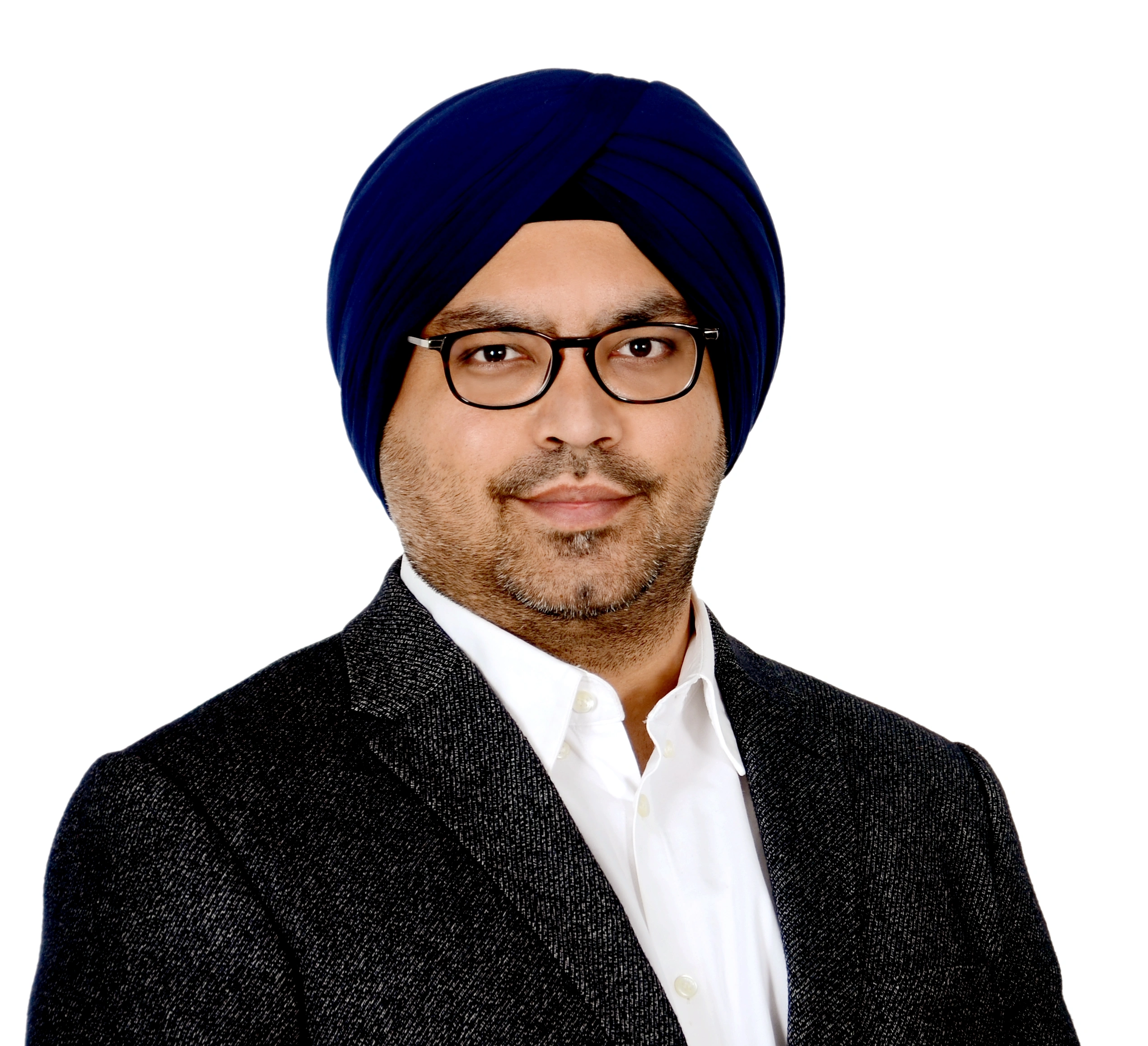
Proper flooring boosts warehouse efficiency, enabling swift movement of goods
Parminder Singh highlights the importance of selecting the right flooring for warehouse operations. Densified concrete or resin-based coatings ensure safety, durability, and efficiency. Concrete flooring supports heavy loads, withstands wear, and provides slip resistance, reducing accidents. It also ensures easy maintenance and a dust-free environment. Epoxy or PU flooring resists chemical spills and supports temperature control, which is crucial for specific storage needs. The right flooring choice enhances long-term cost-effectiveness by minimising repairs and downtime.
Safety Impact
The right flooring enhances worker safety in warehouses with slip-resistant surfaces, reducing falls and accidents. Smooth, well-maintained floors ensure safe movement for foot traffic, forklifts, and MHE, preventing collisions. Additionally, incorporating safety markings and color coding for walkways and storage areas improves visibility and organisation. Overall, the right flooring creates a safer, more secure work environment.
Key Considerations
When choosing flooring for a high-traffic warehouse, consider its load-bearing capacity to support heavy equipment and rack loads. Levelness and flatness increase productivity and reduce accidents. High abrasion resistance ensures durability against wear. Resin-coated flooring offers chemical resistance, protecting against spills and stains, essential for industries like pharmaceuticals, food, and automotive. Densified concrete flooring provides a smooth, dust-free surface for easy cleaning and maintenance. Durable, low-maintenance flooring enhances operational efficiency and safety.
Efficiency Boost
The right flooring significantly improves warehouse efficiency by facilitating fast movement of goods and workers. Level and flat floors reduce accidents with slip-resistant surfaces, minimise floor damage, and reduce maintenance downtime. Poor flooring may necessitate extra MHE purchases, increasing costs. Investing in quality flooring saves money on equipment and repair costs. Easy-to-clean surfaces reduce maintenance time, supporting a safer, more organised warehouse. Overall, proper flooring boosts productivity and operational efficiency.
Specialised Flooring
Different types of flooring are recommended for various warehouse environments. For warehouses with heavy MHEs, concrete floors that comply with standards like TR34 or ACI 302.1R-15 are recommended. In most warehouses, densified surface finishes perform very well. Cold storage facilities require insulation under the concrete flooring and a resin-based surface coating to maintain temperature control and prevent condensation, ensuring efficiency and safety. Chemical-resistant coatings such as epoxy or PU concrete flooring are necessary for warehouses handling hazardous materials, protecting against chemical attacks and other damage. Each flooring type addresses specific operational requirements, enhancing safety, durability, and efficiency tailored to the warehouse’s function.
Cost Consideration
Installing new warehouse flooring is a strategic investment due to its long-term benefits: durability, reduced maintenance, and enhanced safety. A flooring consultant coordinates with geotechnical and structural experts to create durable designs and comprehensive solutions. They prepare construction designs and drawings, considering load requirements, and provide a bill of quantities for tendering. The long-term cost savings and operational benefits justify the initial expense, making it a wise investment.